Angola’s Housing Shortfall Sparks Innovation
Angola is turning to a bold solution to fix its growing housing crisis. A local startup, Power2Build, is using 3D concrete printing to build homes faster, cheaper, and with less labor than traditional methods.
The country has faced a serious housing shortage for years. Back in 2008, Angola launched an ambitious urban housing program. The goal was to build one million homes. But by 2024, only about 220,000 had been delivered.
A Homegrown Startup with Global Tech
Power2Build believes it can help close that gap. The team, made up entirely of Angolan professionals, has partnered with Danish company COBOD. Together, they are bringing some of the world’s largest 3D construction printers to local job sites.
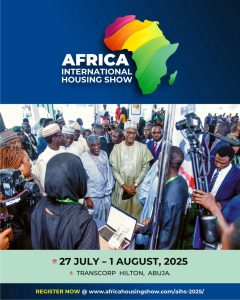
How the 3D Printing Process Works
Instead of using bricks and mortar, these printers build homes layer by layer. First, the building is designed digitally. That design is then sliced into thin layers, which are printed one at a time. Some walls include internal patterns, like honeycomb shapes, to make them stronger.
Another method called tangential continuity helps layers stick better. This creates smoother, more durable walls without weak spots.
Locally Sourced Concrete for Custom Builds
To print the walls, Power2Build uses a special concrete mix. It includes local materials like sand and gravel. They also add cement, hardeners, and flow-control additives. This mix is pumped through a large nozzle that moves automatically along a programmed path.
Precision Printing with Powerful Machines
Depending on the setup, the nozzle is guided by a gantry system or a robotic arm. The gantry moves the nozzle in straight lines across three directions. Robotic arms give more flexibility, allowing for complex shapes and designs.
This system cuts down on manual labor. There’s less need for bricklayers, but more demand for skilled operators and planners.
Massive Machines Reshape Housing
The equipment is also impressive. Power2Build is using COBOD’s BOD2 series—currently the second-largest 3D construction printer in the world. These machines can build homes up to 10 meters tall, 15 meters wide, and 45 meters long. They work at speeds of up to 500 millimeters per second. Setup time takes just a few hours.
An even newer model, the BOD3, offers even more flexibility. It can print up to 15 meters high and allows for faster setup and breakdown.
Looking Ahead: Sustainable and Affordable Living
The team is not stopping there. Power2Build is already exploring new materials like clay and soil-cement blends. These could make 3D-printed housing more affordable for low-income families.
A Global Shift in Housing Solutions
Around the world, cities are also looking for creative ways to fight the housing crisis. Los Angeles is turning empty buildings into apartments. Spain is testing new housing models focused on community living. In Germany, residents are even helping design their own homes from the start.
In Angola, the answer might come from machines—not bricks. With every layer printed, Power2Build is building more than just walls. They’re building a new future for housing in Africa.